WHAT IS SPIRAL WOUND LINING TECHNOLOGY?
Spiral Wound Lining technology represents a sophisticated trenchless rehabilitation method that involves the underground assembly of a modular winding machine within the host pipeline. The system utilizes prefabricated PVC-U strip profiles and stainless steel bands, which undergo rigorous quality inspection before being fed into the winding mechanism. The installation process synchronizes the spiral winding of both materials, with the PVC-U profiles' specially designed interlocking edges forming a continuous, structurally independent composite pipe within the existing conduit. Once the liner is installed, our self-developed high-strength non-shrinkage grouting material is injected into the gap between the original pipeline and the iliner, ensuring a complete seal and enhancing the structural integrity of the new liner. This innovative approach creates a high-strength, watertight steel-reinforced polymer liner that effectively renews the pipeline's structural integrity.

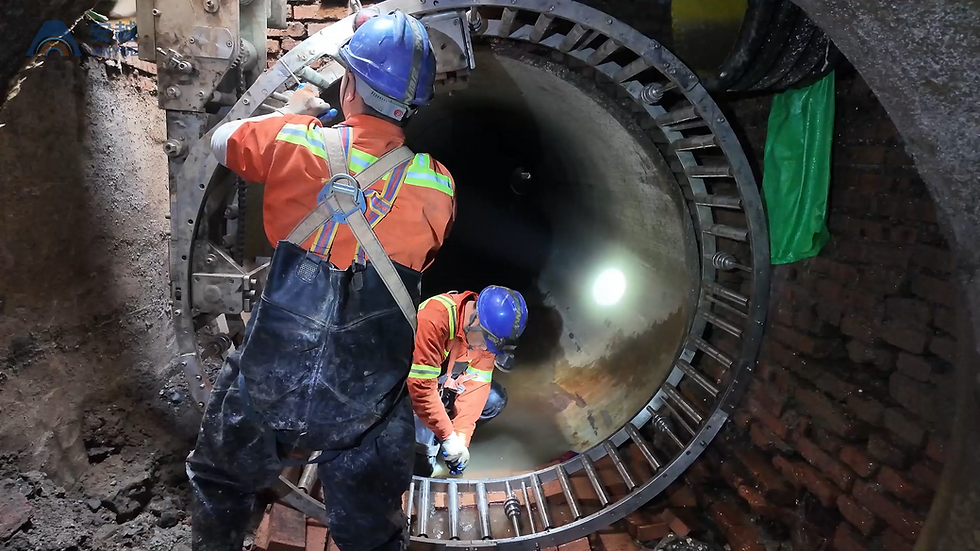

Overview
SPIRAL WOUND LINING TECHNOLOGY
Diameter Range: DN800 to DN3000 (with potential for larger diameters through custom engineering)
Applicable Pipeline Types:
1. Gravity drainage systems (stormwater and sanitary sewers)
2. Large-diameter conveyance pipes
3. Box culverts and arch structures
4. Concrete, PVC, and other common pipe materials requiring rehabilitation

Two Methods of Spiral Wound Lining Installation:
1. Fixed-Head Winding Method
The winding machine remains stationary in the working shaft during operation. As the PVC profile and steel band are spirally wound, the entire newly formed pipe progressively advances along the pipeline's axial direction. This method is particularly suitable for projects with stable working shaft conditions.
2. Mobile-Head Winding Method
The winding machine is initially positioned at the end of the pipe section to be rehabilitated. During the winding process, the machine moves forward along the pipeline as it simultaneously constructs the new liner. This approach offers greater flexibility for projects with space constraints or complex layouts.
Technical Features:
1. The technology allows construction with water flow present requiring minimal pipeline drainage.
2. The smooth repaired pipe wall significantly improves water flow capacity.
3. It effectively repairs various structures including large pipes and box culverts across different materials.
4. The chemical-free installation process eliminates environmental contamination risks.
5. Construction adapts to challenging environments and long-distance pipeline applications.
6. The flexible liner accommodates diameter variations, bends and misaligned joints even under dynamic loads.
7. Prefabricated components enable fast and reliable on-site assembly unaffected by external factors.
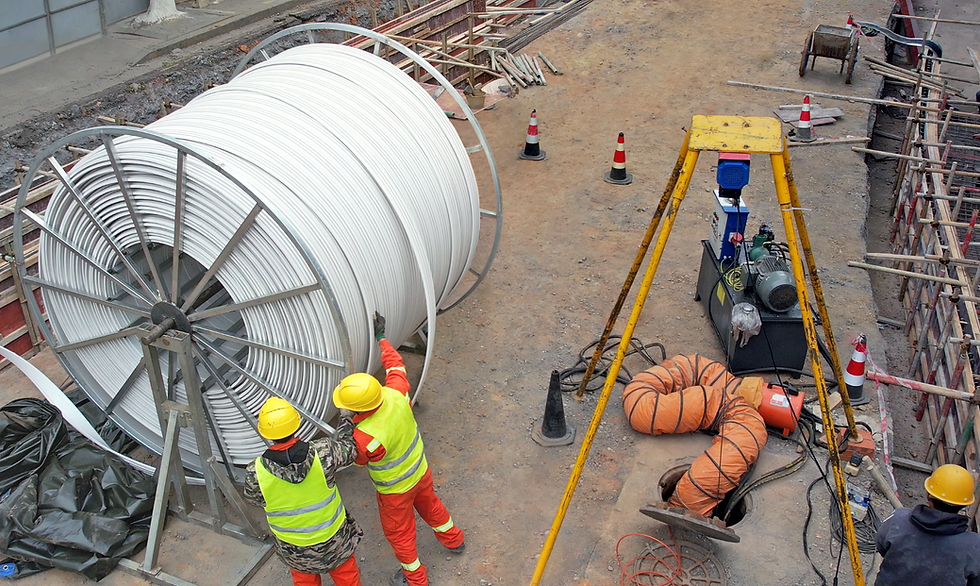
Lining Process
Key Features
Water-Tolerant Installation
Eco-Friendly Chemical-Free Process
Broad Material And Structure Applicability
Enhanced Flow Capacity
Flexible Load-Bearing Rehabilitation
Adaptable To Complex And Long-Distance Projects
Our Products

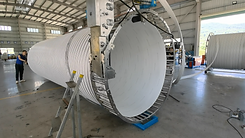

ANYUE Spiral Wound Liner
-
PhD-led R&D team drives continuous product innovation through independent technological development.
-
Proprietary T-shaped double-lock winding profile ensures structural strength and superior sealing performance.
-
Self-developed spiral winding machines cover fixed-head, mobile-head, and non-circular cross-section configurations.
-
Advanced leak-proof solutions with proprietary non-shrink grouting materials and layered injection technology.
-
Extensive field experience supports complex projects through customized training and on-site guidance.
-
Comprehensive trenchless package integrates materials, equipment, and construction expertise for turnkey delivery.
Test Item | Test Result | Test Standard |
---|---|---|
Flexural Modulus | >2640 MPa | ASTM F1697-18 |
Flexural Strength | >36 MPa | ASTM F1697-18 |
Tensile Strength | >42 MPa | ASTM F1741-18 |




ANYUE Spiral Wound Equipment
-
The fixed-head spiral winding machine is designed for the rehabilitation of circular pipes with diameters ranging from DN800 to DN3000mm.
-
The mobile-head winding equipment is capable of repairing both pipes and box culverts with diameters between DN1500 and DN4000mm.
-
Featuring an innovative design, the mobile-head winding equipment can adapt to various pipe cross-sectional shapes and sizes by simply replacing the track, enabling versatile spiral winding repairs.
-
The optimized strip profile cross-section design, combined with reinforced stainless steel winding strips, ensures a lining structure with superior hoop strength.
-
Our proprietary high-strength, non-shrink grouting material delivers exceptional strength, dimensional stability, underwater cohesion, and flowability, guaranteeing high-quality annular grouting.
-
The finished lining surface is smooth and offers excellent corrosion resistance.
-
The embedded steel ribs on the liner's exterior, together with the grout, form a stable composite structure upon curing, ensuring long-term structural integrity after repair.
Item | Specification |
---|---|
Stainless Steel Strip Forming Equipment | GD-86 |
PVC Liner Reel | Self-designed |
Hydraulic System | 11KW |
Mobile Head Winding Machine | Pipe diameter DN1500-DN4000mm |
Fixed Head Winding Machine | Pipe diameter DN800-DN3000mm |
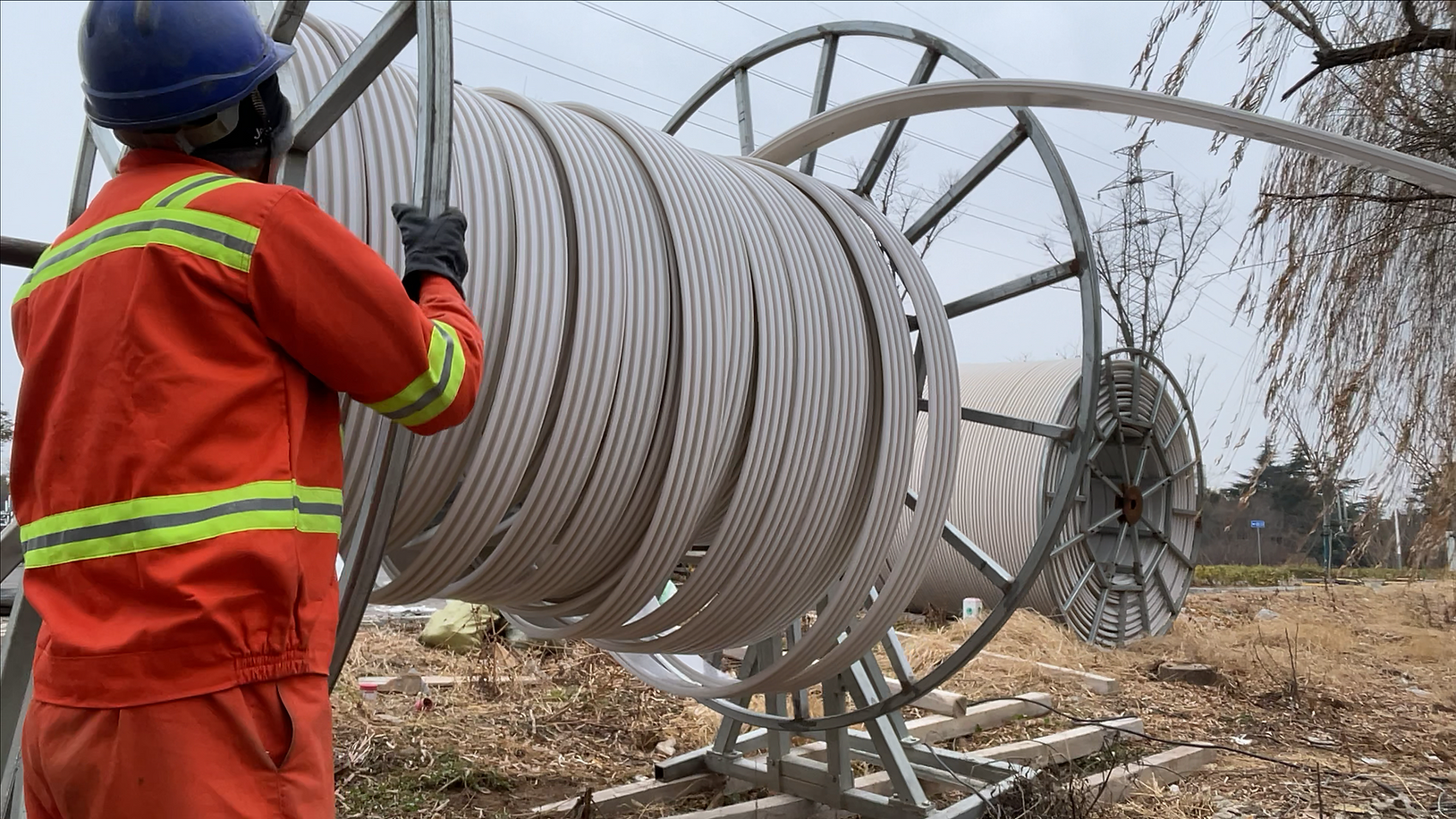

Fixed

Mobile
Case Study
DN2000 ROAD WATER ACCUMULATION POINT RENOVATION PROJECT IN JIUJIANG
Project Overview:
Our team recently completed the rehabilitation of a severely deteriorated DN2000 pipeline exhibiting settlement, deformation and multiple fractures. Despite these challenges and the pipeline's large diameter, we successfully executed the repairs while maintaining continuous service - a significant achievement in trenchless pipeline rehabilitation.
We employed advanced spiral wound lining technology to install a durable PVC-stainless steel composite liner within the existing pipe. This innovative approach allowed us to correct structural defects without excavation while operating under tight urban constraints. The entire process was completed without interrupting service, demonstrating the effectiveness of modern trenchless methods.