Spiral Wound Lining Technology: An Advanced Solution For Pipeline Rehabilitation
- Layla Tong
- Apr 1
- 2 min read
Mechanical Spiral Wound Lining (SWL) technology represents a sophisticated trenchless rehabilitation method that involves the underground assembly of a modular winding machine within the host pipeline. The system utilizes prefabricated PVC-U strip profiles and stainless steel bands, which undergo rigorous quality inspection before being fed into the winding mechanism.
The installation process synchronizes the spiral winding of both materials, with the PVC-U profiles' specially designed interlocking edges forming a continuous, structurally independent composite pipe within the existing conduit. This innovative approach creates a high-strength, watertight steel-reinforced polymer liner that effectively renews the pipeline's structural integrity.
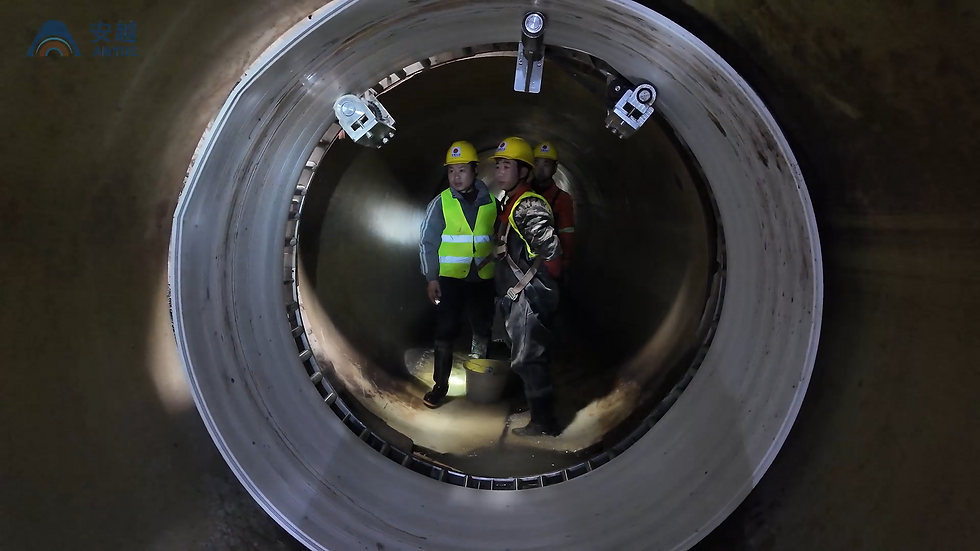
Technical Specifications
Diameter Range: DN800 to DN3000 (with potential for larger diameters through custom engineering)
Applicable Pipeline Types:
Gravity drainage systems (stormwater and sanitary sewers)
Large-diameter conveyance pipes
Box culverts and arch structures
Concrete, PVC, and other common pipe materials requiring rehabilitation
Key Technical Advantages
1. Water-Tolerant Installation Capability
Enables rehabilitation without complete flow interruption.
Operational in pipelines with up to 30% continuous flow.
Eliminates the need for costly bypass pumping systems.
2. Geometric Adaptability
Compensates for joint misalignment (up to 15% of pipe diameter).
Accommodates diameter variations and non-circular profiles.
Suitable for ovalized or deformed pipe sections.
3. Structural Performance Characteristics
Withstands dynamic loading conditions (HS-20 compliant).
Performs reliably in poor geological conditions.
Demonstrates exceptional resistance to ground movement.
4. Installation Flexibility
Effective in challenging environments (urban, ecologically sensitive areas).
Capable of long-distance rehabilitation (500+ meter continuous runs).
Minimal surface disruption during implementation.
Engineering Benefits
The technology offers significant advantages over conventional rehabilitation methods:
Immediate structural capacity post-installation (no curing period required).
Superior hydraulic characteristics with a smooth interior surface.
Corrosion-resistant materials ensure extended service life.
Reduced carbon footprint compared to open-cut replacement.
Quality Assurance
All materials comply with international standards:
PVC-U profiles meet ISO 16422 specifications.
Stainless steel components satisfy ASTM A240 requirements.
Final product exceeds ASTM F1216 performance criteria.
Comments